Alfa Laval PX 115e & PX 115eEX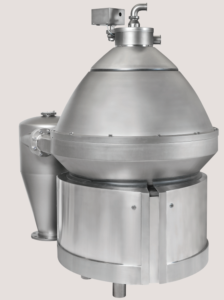
The Alfa Laval range of centrifuges for the vegetable oil and animal fat refining industries is continuously modernized to take advantage of developments in materials, mechanical design and fluid dynamics. The PX 115e/115eEX is a largesized machine equipped with the direct drive system eDrive™.
Applications
Continuous degumming, neutralizing, dewaxing, and washing of fatty oils, such as various vegetable oils, lard, tallow, and fish oil.
Standard design
The machine consists of a frame with a base that contains a hollow vertical bowl spindle, on which the rotor part of the electric motor is mounted. The motor stator is placed inside the bottom part of the frame. The bowl is fixed on top of the spindle inside the space formed by the upper part of the frame, the solids collecting cover and the frame hood. The hood carries the liquid discharge system.
All parts in contact with the process liquid are made of stainless steel. The bowl is of the solids-ejecting type with an automatic hydraulic operating system for intermittent solids discharge. In the eDrive™ system, the electric motor is a switched reluctance motor with a permanent magnet rotor. The motor is powered by a frequency inverter.
Design features
Inlet. The PX 115e/115eEX is based on a unique, semihermetic design concept. The hermetic, bottom-fed inlet ensures a gentle, non-destructive acceleration of the feedstock up to full bowl speed. This minimizes drop splitting and maximizes separation performance. The flow area for the feedstock has been increased to minimize inlet pressure drop.
Outlets. The outlets on the heavy and light phases are open, reducing the pressure drop across the separator. The feed-pressure requirement of the machine is therefore low. The outlets are equipped with stationary paring devices for removal of the different phases. The paring disc on the light phases is fixed, while the paring tubes on the heavy phase are adjustable.
Centrizoom™. By adjusting a positioner on the heavy-phase outlet, the operator can reduce or extend the paring diameter of the paring tubes. This patented innovation, Centrizoom™, makes it possible to adjust the interface between oil and soapstock in the bowl during operation to obtain maximum separation efficiency.
Low noise level. With the working environment in mind, the PX 115e/115eEX is designed to operate at low noise levels. This is achieved through a rubber-damped bearing assembly, jacketed frame and an outer bowl design which is engineered for low wind noise.
Energy savings. The eDrive™ electric motor is placed between the bearings in the bearing system that is well proven for more than two decades. The motor type has a higher efficiency than conventional induction motors, which means energy savings of 10-15% in combination with the absence of a mechanical gear. The motor is water cooled and controlled by frequency inverter.
Small footprint. The compact design of eDrive™ means a small footprint and saving of valuable floor area.
Lubrication system. The lubrication system consists of tank, heat exchanger, pump and filter.
Control and supervision. A 2Touch service panel controls and/or supervises the following functions:
• Cooling of motor and bowl casing.
• Cooling and lubrication of mechanical seals.
• Flushing of outside of bowl and inside of bowl casing.
• Control of the frequency converter and the bowl speed.
• Control and supervision of lubrication and bearing temperatures.
• Control and supervision of discharge system.
• Supervision of vibration.
• Communication with plant control system via Modbus TCP.
The controller program is built in modules for easy incorporation of different combinations of functions.