Alfa Laval OFX X20
The Alfa Laval X20, model OFSX 520S-71CEGPX, is a high capacity concentrator designed for de-oiling of produced water. The design is based on the robust nozzle-type disc bowl centrifuge in order to withstand the demanding conditions in the oil-producing industry. The machine is in compliance with the EC ATEX directive category 2, and therefore Zones 1 and 2.
As an option, the machine can be operated under a positive pressure of 400 kPa, as it has an ASME-approved pressure casing. The X20 concentrator is one machine in the X20 family, which also consists of machines for applications such as heavy crude and tar sand dehydration.
Applications
The X20 concentrator is designed to reduce the oil content to 15 ppm or lower in produced water. Using a centrifuge for this application is especially suitable for:
– heavy crude oil facilities
– gas production facilities with associated condensate
– deepwater offshore facilities including floating platforms
The compact design makes it especially useful for offshore processing, including at floating platforms where the sea heave may cause problems for conventional technology.
Standard design
Separation takes place in the bowl, which is placed on a vertical spindle. An electric motor mounted vertically drives the spindle near the bottom via a flat belt. Circulating oil ensures that the bearings are lubricated. An external lube oil pump maintains the necessary pressure. The centrifuge motor is designed for variable frequency drive.
All metallic parts that come into contact with the process liquid are made of high-grade stainless steel. Liquid-wetted gaskets are made of fluorocarbon rubber.
To recover energy from the discharged nozzle flow, the nozzles are placed in the bowl periphery at a narrow angle from the tangent. The eighteen nozzles can be reached from the outside via a hatch in the frame hood, which allows technicians to replace them easily and rapidly without dismantling the frame. The nozzles are made of tungsten carbide, suitable for abrasive solids. The solids collecting ring is fitted with a wear liner made from polyurethane.
The inlet and outlets are fitted with ANSI flanges. A rotating face seal seals off the bowl casing from the bearings. A cover interlocking kit makes it impossible to start the centrifuge unless it is properly assembled.
Special features
The atmospheric version of the X20 concentrator is fitted with a power recovery device on the water outlet. The pressurised version OFSX 520T-71CEGPX has a paring disc, which eliminates the need for an external water pump.
Basic equipment
Centrifuge with motor, set of tools, speed and vibration sensors, oil pressure switch, temperature sensors for the main spindle bearing and the motor winding, vibration dampening feet, foundation plate and standard set of spares.
Options
The X20 concentrator can be fitted with a nozzle monitor. This consists of a sensing device, which is hit by the jet from each individual nozzle. The signal is then transmitted to a box, which displays the result. The monitor shows whether the nozzles are clogged or worn out, therefore enabling safe operation and high availability.
The machine can be supplied with a pressurised bowl casing, design pressure 400 kPag. The separated water leaves the centrifuge under pressure. It is usually supplied as a functioning unit with a process liquid module, starter and controls. In cases where flammable liquids are processed, an inert gas system is provided with controls integrated in the machine controls.
Operating principles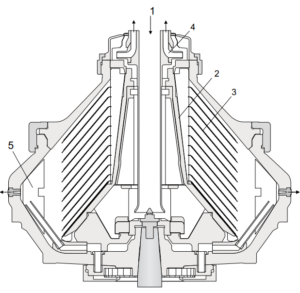
The feed is introduced to the rotating centrifuge bowl from the top via a stationary inlet pipe (1), and is accelerated in a distributor (2) before entering the disc stack (3). Separation takes place between the discs. The oil phase moves through the disc stack towards the centre of the bowl, and is pumped out under pressure by means of a built-in paring disc (4). The solids are collected at the bowl periphery and continuously discharged through the nozzles together with some water. The water droplets move towards the periphery to the oil/water interface where they coalesce to form a continuous water phase. The water that does not pass out through the nozzles is collected in pipes leading towards the centre
through the bowl bottom into a chamber from where the water is pumped out under pressure by a paring disc. If the water flow is insufficient to satisfy the nozzle demand, water is imported into the bowl backwards through the paring disc by the OPTIPHASER™ system, ensuring no loss of oil through
the nozzles. Filler pieces (5) prevent build-up of the solids between the nozzles and consequently no solid cones can build up that collapse over the nozzle, blocking and disturbing normal production.
Utilities consumption
Electric power | max. 96 kW |
Safety water | 43–55 m3 /h (190–240 US gpm) |
Inert gas blanketing | approx. 0.4 Nm3 /h |
Inert gas initial purging | approx. 4 Nm3 |
Material data
Bowl body, hood and lock ring | s.s. 1.4501 UNS 32760 |
Solids cover and frame hood | s.s. 1.4401 UNS 31600 |
Frame bottom part | grey cast iron |
In and outlet parts | s.s. 1.4401 UNS 31600 |
Gaskets and O-rings | Fluorocarbon rubber |
Connections
Feed | 3½” flange ANSI |
Oil outlet | 3½” flange ANSI |
Water outlet | 2” alt. 3” flange ANSI (3” for pressurised vers.) |
Solids outlet | 6” flange ANSI |
Shipping data
Centrifuge incl. bowl and motor | 4,580 kg (10,100 lbs) |
Bowl | 1,050 kg (2,350 lbs) |
Motor | 1,180 kg (2,600 lbs) |
Gross weight | 4,900 kg (10,800 lbs) |
Volume | 8.0 m3 |
Technical specifications
Throughput capacity | max. 190 m3 /h (840 US gpm) |
Water flow | max. 60 m3 /h (260 US gpm) |
Oil flow | max. 190 m3 /h (840 US gpm) |
Nozzle flow | max. 30 m3 /h (130 US gpm) |
Bowl volume | 70 l |
Bowl speed | 3,750 rpm |
Motor speed, synchronous. 50/60Hz | 1,500/1,800 rpm |
Motor power installed | 152 kW |
Centrifugal force inside bowl | max. 6,480 g |
Starting time | 5–8 mins |
Stopping time without brake | 80 mins |
Stopping time with brake | 6–7 mins |
Feed temperature range | max. 110 °C (230 °F) |
Feed inlet pressure required at inlet flange | min. 100 kPa |
Outlet pressure of oil at outlet flange | 500 kPa |
Outlet pressure of water at outlet flange | 600 kPa |
Sound pressure | 82 dB(A) |