Home » Separators » Alfa Laval Separators »
Alfa Laval BTPX 710 Separator
Applications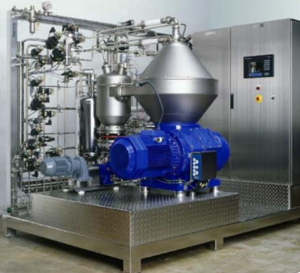
The BTPX 710 module is based on the solids-ejecting centrifuge BTXP 710SGD-34CDP in clarifier execution. It is equipped with a double axial spindle seal and timer-triggered solid discharge. It is used for removing suspended solids with particle sizes from approximately 0.5 to 500 µm from a liquid having a lower specific gravity than the solids. The solids content in the feed is normally in the range of 0.1-10% by volume.
The main applications are bacteria, rDNA products, enzymes, growth factors, cell cultures and vaccines.
Special features
The BTPX 710 has a timer-triggered partial discharge system, meaning that only part of the bowl content is emptied during discharge. The discharge takes place at full speed without any interruption of the feed.
The inlet of the separator is equipped with wing type distributor or a low shear disk inlet, which enables separation of products with foaming tendency or high sensitivity to shear. The flanged motor is direct coupled to the drive system. The drive system is splash lubricated without any need for an external lubrication circuit.
All product wetted surfaces are in high grade stainless steel with a standard surface finish of less then 1.2 micron Ra. Finer finish is available on demand. The bowl casing, cyclone and cooling jackets are pressured rated to 3 bar. The Separator can be steam sterilised up to 1300. The separator can be mounted in a fully contained system with no risk for product or environmental contamination. The built-in paring disc for the liquid phase eliminates the need for an external pump. The machine is equipped with nozzles for flushing above the bowl and in the sediment oulet.
Standard design
All liquid-wetted parts are in high-grade stainless steel and liquid-wetted rubber gaskets in FDA approved EPDM. The centrifuge is available with main connections as sanitary flanges and all other utility connections clamp type. The centrifuge can be equipped with sensors for monitoring vibration level, and a cover switch to be used for preventing the motor from being started unless the centrifuge top part has been properly mounted. The centrifuge is equipped with anchoring feet and vibration dampers.
Operating principles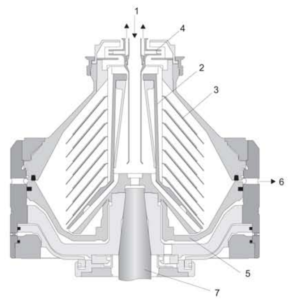
The feed is introduced to the rotating centrifuge bowl from the top via a stationary inlet pipe (1), and is accelerated in a distributor (2) before entering the disc stack (3). It is between the discs that the separation takes place. The liquid phase moves towards the centre of the bowl, from where it is pumped out under pressure by means of a build-in pairing disc (4). The heavier solids phase is collected at the bowl periphery, from where it is discharged intermittently via the centrifuge cyclone. The solids discharge is achieved by a hydraulic system below the separation space in the bowl, which at certain intervals forces the sliding bowl bottom (5) to drop down, thus opening the solids ports (6) at the bowl periphery. The bowl is mounted on a vertical spindle (7) driven by a horizontally mounted motor, via a worm gear.
Ultilities consumption
Electric power | 15 – 20 kW |
Operating liquid + seal water | 120 dm3/h + 1 – 2 dm3/discharge |
Flushing liquid | 2 – 20 dm3/discharge |
Cooling air | 500 dm3/ discharge |
Air | 2 Nm3/h |
Dimensions
Technical specification
Max. throughput capacity | 10 m3/h |
Max. solids-handling capacity | 360 dm3/h |
Feed temperature range | 0 – 100 °C |
Feed inlet pressure require | 0 – 200 kPa |
Liquid outlet pressure available | 300 kPa |
Installed motor power | 22 kW |
Noise level (ISO 3744 or 3746) | 76 dB |