Home » Separators » Alfa Laval Separators »
Alfa Laval AFPX 610 Separator
High g-forces, high demands on clarification capacity and outstanding reliability –These are the main criteria that have formed the basis for the design of the new AFPX 610 centrifuge.
Applications
The AFPX 610 is a solids ejecting disc stack centrifuge designed for intermittent discharge of solids, while splitting a tight emulsion of two liquids. It is mainly used in the animal and fish processing industry, where it is used for a number of different separation and purification duties, such as:
– Meat and fish extract
– Gelatine clarification
– Fats and oils purification
Special Features
The AFPX is designed to separate at a very high g-force to improve purification and clarification of any feed. The device that accelerates the feed up to the speed of the rotor, is specially designed to do so in a gentle manner, which further helps to increase the separation performance. The outlet of the AFPX 610 is designed to give the oil phase a final polish. When the oil phase is sprayed out into the collecting frame, the last traces of water is separated from the oil phase by evaporation.
Standard design
The bowl is mounted on a vertical spindle that is driven via a clutch and a worm gear. The bottom part of the machine forms a housing for the worm gear, where also the oil bath is contained.
The upper part of the machine, the frame, carries the inlet device and is equipped with connections to transport the separated liquids away from the machine.
All liquid wetted parts are made in high-grade stainless steel. The design conforms with a number of EC directives and the machine is made in accordance with the general directives for machinery. The machine is available in purifier or concentrator execution.
Standard equipment
Separator with feed and discharge devices, vibration dampers, earth connecting kit, vibration switch, temperature sensor for motor winding, speed sensor, cover interlocking kit, standard set of spare parts, set of tools, revolution counter, set of erosion protecting parts and flange motor.
Auxiliary equipment
Process components including in- and outlet pipes, valves and flexible connections. Programmable logic control unit. Starter for electric motor.
Operating principles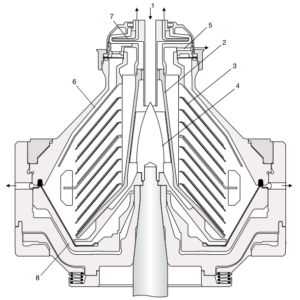
Separation takes place inside a rotating bowl. The feed is introduced to the rotating centrifuge bowl from the top via a stationary inlet pipe (1), and is accelerated in the distributor (2), before entering the disc stack (3). The distributor is designed especially to ensure smooth acceleration of the feed liquid (4). The separation of liquid-liquid-solids takes place between the discs, with the oil phase moving through the disc stack to the centre and is discharged through pipes (5) and sprayed out into the collecting frame. The water and solids separated from the oil moves out to the periphery, the water is led via channels in the top disc (6) to the paring chamber, where it is pumped out of the rotor with means of a built-in paring disc (7). The solids are collected in the periphery, from where it is discharged intermittently via the centrifuge cyclone. The solids discharge is achieved by a hydraulic system which at preset suitable intervals forces the sliding bowl bottom (8) to drop down and thus opening the solids ports at the bowl periphery.
Utilities consumption
Electric power | Max 19 kW |
Shipping data
Centrifuge excl. bowl and motor | 897 kg |
Motor | 124 kg |
Bowl | 235 kg |
Gross weight (approx.) | 1300 kg |
Volume | 5.0 m3 |
Dimensions
Technical specification
Max throughput capacity | 20 m3 /h |
Feed inlet pressure | 0 – 1.8 bar |
Feed temperature range | 0 – 100 °C |
Max density sediment/feed | 1296/1100 kg/m3 |
Water outlet pressure | Max 10 bar |
Motor power | 18.5 kW |
Motor speed synchronous | 69 Hz 2070 rpm |
Starting time | >14 min |
Stopping time brakes/roll-out | > 7 / > 50 min |
Sound pressure | > 79 dB(A) |
Centrifugal force (sludge space) | 11600 g |