APV/SPX DW Series Rotary Pump
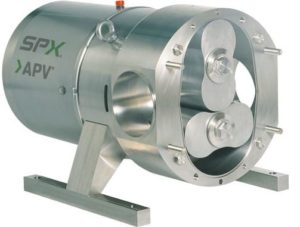
Engineering excellence, allied to stringent quality control, ensures that SPX’s unrivaled range of APV products complies with the highest international standards for hygiene. In the light of growing pressure worldwide to deliver safe, high quality food, all SPX products are designed for easy clean ability, while minimizing the use of valuable resources, such as energy. The APV product portfolio includes a wide range of pumps, valves, heat exchanges, mixers and homogenisers designed for use in the food, dairy and beverage, as well as in chemical, personal care, pharmaceutical and other liquid process industries.
This series was previously the Howard Cleanline range.
Features and Benefits
High Volumetric Efficiency
The DW range is designed for outstanding efficiency. Internal clearances have been minimized so that a smaller pump size can be selected for medium viscosity applications. This reduces both the initial investment and running costs.
Ultra-Hygienic, Accommodates Harsh CIP-Cycles
All DW models are CIP/SIP cleanable. The pumps are designed to withstand rapid temperature changes and can therefore accommodate very harsh CIP cycles.
Pulse-Free Performance
When pumping highly viscous products, the DW pump with piston rotors runs completely pulse-free. This ensures a consistent process flow, which is required in connection with filling machines. It also safeguards valves, and other equipment that can be damaged by pressure surges.
Low NPSH-Requirement
The highly improved suction capability of the DW pump considerably reduces the NPSH-requirement. This in combination with the absence of pressure pulsations makes the DW pumps ideal for many applications, such as ultra filtration.
Gentle Product Handling
The rotor designs available ensure maximum product integrity and minimize risk of potential damage to sensitive products. Both piston and bi-lobe rotors are suitable for high and low viscosity. They will also handle cheese curds and whey, soft fruit and meat — which previously involved fitting special rotors.
Easy Maintenance
The easy-to-access front loaded mechanical seals reduce maintenance time considerably. All shaft seal O-rings are identical, and access to the shaft seal is achieved by simply removing the front cover and the rotors. Likewise, the timing of rotors is an equally uncomplicated operation.
Low Noise Levels
The patented rotor design practically eliminates hydraulic noise and the helical gears minimize gearbox noise.
Global Design
The entire range complies with the European EHEDG and the American 3-A hygiene standards.
High Capacity
The DW6 high capacity pumps are unique in the field of positive displacement pumps. They are capable of running up to 800 rpm and pumping up to 1,016 liters/100 revs (268 gal/100 revs), approximately 370 m3/h (1,628 gal/min).
Theory of Operation
DW pumps are positive-displacement, low-slip, stainless steel pumps designed with larger diameter shafts for greater strength and stiffness, mounted on a heavy-duty cast iron bearing frame (stainless steel option available) with double-tapered roller bearings.
Expanding cavities are formed at the inlet drawing the liquid into the rotors. Meshing of the rotors forces the fluid out of the pumping chamber.
Typical Product Applications
Beverage:
- Fruit Juice
- Cider and Wine
- Yeast
- Liquid Sugar and Glucose
Food:
- Fruit Preserves
- Soups and Sauces
- Baby Food
- Chocolate
Pharmaceutical and Toiletries:
- Antibiotics
- Toothpaste
- Cough Medicine
- Shampoo
Dairy:
- Cream
- Butter
- Yogurt
- Ice cream
- Cheese Curd & Whey
Chemical:
- Paint
- Oil Additives
- Resins
- Photographic Film Coatings
Product Specifications
The DW pump is designed for ultra-hygienic applications. The range consists of 26 models with capacities ranging from 3 liters/100 revs to 1,016 liters /100 revs (0.8 gal/100 revs to 268 gal/100 revs) and pressures up to 30 bar (435 psi). All product contact parts are made from AISI 316L stainless steel and all elastomers comply with FDA-requirements.
There are two rotor types (piston and bi-lobe) available. The piston rotors can be easily changed to bi-lobe rotors with out changing the rotor case. The porting on the pump can also be changed from horizontal to vertical (and vice versa) without any modification to the pump or use of a special gear case assembly.
Maximum Displacement | Maximum Pressure | ||
Model Number | Rotor Type | Litres/100 Revs
(Gal/100 Rev) |
Bar
(PSI) |
DW1/003/7.5 | Piston | 3 (0.8) | 7.5 (109) |
DW1/004/15 | Bi-lobe | 4 (1.1) | 15 (218) |
DW1/007/7 | Bi-Lobe | 7 (1.8) | 7 (102) |
DW2/006/10 | Piston | 6 (1.6) | 10 (145) |
DW2/007/20 | Bi-Lobe | 7 (1.8) | 20 (290) |
DW2/013/10 | Bi-Lobe | 13 (3.4) | 10 (145) |
DW3/014/10 | Piston | 14 (3.7) | 10 (145) |
DW3/017/20 | Bi-Lobe | 17 (4.5) | 20 (290) |
DW3/030/10 | Bi-Lobe | 30 (7.9) | 10 (145) |
DW3/050/5 | Bi-Lobe | 50 (13.2) | 5 (73) |
DW4/033/10 | Piston | 33 (8.7) | 10 (145) |
DW4/039/20 | Bi-Lobe | 39 (10.3) | 20 (290) |
DW4/073/10 | Bi-Lobe | 73 (19.3) | 10 (145) |
DW4/125/5 | Bi-Lobe | 125 (33.0) | 5 (73) |
DW5/080/12.5 | Piston | 80 (21.1) | 12.5 (181) |
DW5/093/25 | Bi-Lobe | 93 (24.6) | 25 (363) |
DW5/142/15 | Bi-Lobe | 142 (37.5) | 15 (218) |
DW5/256/7 | Bi-Lobe | 256 (67.6) | 7 (102) |
DW6/172/12.5 | Piston | 172 (45.4) | 15 (218) |
DW6/198/30 | Bi-Lobe | 198 (52.3) | 30 (435) |
DW6/308/15 | Bi-Lobe | 308 (81.4) | 15 (218) |
DW6/519/07 | Bi-Lobe | 519 (137.1) | 7 (102) |
Options and Accessories
Standard elastomer material is EPDM. FPM and Isolast (perfluoroelastomer) are also available.
The standard connections are S-Line. Other sanitary and industrial fittings are available.
Rotor Options
The two rotor types, which are available in three different versions, are suitable for product temperatures up to 110°C (230°F).
- Multi Duty Rotors are standard rotors suitable for most applications. The clearance is greater than that of the high efficiency rotors.
- High Efficiency Rotors are designed for low viscosity products. The size of the rotors has been increased and the clearance is minimal.
- NGA Rotors are made of Non Galling Alloy (W88) for use with low viscosity products. The material allows the rotors to touch the pump housing with out damaging the housing or the rotors. Low tolerances may therefore be applied without decreasing the reliability.
- The bi-lobe rotors can be supplied as “high temperature” rotors, suitable for product temperatures up to 180°C (356°F). The rotors are smaller for expansion due to the temperature.
Design | Features | |||||
Rotor Types | Material | Clearance | Maximum Temperature Shock | Maximum Difference in Pressure (% of Pump Maximum) | Fully Positive | Vulnerability towards Foreign Matters bigger than Clearance |
Multi-Duty | 316L | Medium | 130°c | 110°c (100%) | 500cp | High |
High Efficiency | 316L | Small | 110°c | 50°c (100%) | 300cp | High |
High Efficiency | NGA | Small | 180°c | 80°c (100%) | 300cp | Low |
Super Tight | NGA | Very Small | 180°c | 80°c (80%) | 100cp | Low |
High Temperature | 316L | Large | 180°c | 120°c (100%) | 700cp | High |
High Temperature | NGA | Large | 210°c | 180°c (100%) | 700cp | Low |
Special Application Options
- Rectangular Inlet for extremely high viscosity products. By applying a rectangular inlet, the inlet conditions are considerably improved.
- Thermal Jacket to provide a constant temperature level within the pump. This may be the solution for handling temperature-sensitive products such as chocolate.
- Relief Valve releases pressure within the pump when it becomes too high. The relief valve is needed if no other safety devices are installed.